En ny svejsemetode muliggør reparation af store støbejernskomponenter i vindmøller. Teknologien har potentiale til at reducere både tid, omkostninger og CO2-udledning i vindenergisektoren.
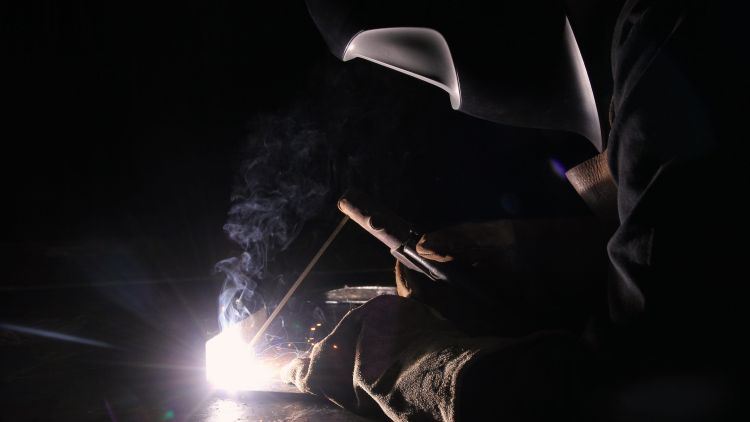
Udfordringen for industrien er, at store støbejernskomponenter i vindmøller ikke blot er dyre, men også vanskelige at reparere, hvis der opstår defekter under støbningen. Derfor kasseres mange støbte dele. Med stigende møllestørrelser har mange støberier svært ved at imødekomme efterspørgslen, hvilket gør svejsning til et attraktivt alternativ til at reducere omkostninger og udvide leverandørbasen.
Et innovationsprojekt har nu udviklet en ny svejsemetode, der er målrettet til at reparere defekte vindmøllekomponenter. Teknologien har potentiale til at reducere både tid, omkostninger og CO2-udledning i vindenergisektoren.
Teknikken er et resultat af innovationsprojektet WeldCast, som har samlet partnerne Siemens Gamesa Renewable Energy, Vestas Wind Systems, FORCE Technology, DTU og Baettr. Projektet er støttet af Innovationsfonden og faciliteret af Energy Cluster Denmark.
Hans-Frieder Vogt, Team Lead Structural Analysis hos Siemens Gamesa, er glad for samarbejdet:
-Vi har set, at vi kan diskutere detaljer åbent uden at kompromittere vores konkurrenceposition og – lovgivning. Jeg tror, at nøglen til det godt samarbejde og fælles løsninger er, at vi deler mange af de samme udfordringer.
Identificer, kategoriser og reparer jernkomponenter
Den nye svejseteknologi forenkler reparationsprocessen og reducerer både spild og produktionstider.
-Vi har nu en bedre forståelse af, hvordan vi identificerer og kategoriserer defekter og hvordan vi reparerer dem, siger Anders Vedel, Chief Science Advisor hos Vestas.
Kaare Jensen, Senior Welding Technician hos FORCE Technology, forklarer:
-Vi har udviklet et mellemlag, der tilpasser sig svejsningens ændringer og fylder det med et andet materiale, hvilket gør det muligt for os at lave svejsninger uden revner eller defekter.
Den nye teknologi kan føre til en mere ressourceeffektiv vedligeholdelse af møller, og dermed reducere omkostningerne og tiden, der bruges på at reparere store komponenter. Selvom resultaterne er lovende, er der stadig et stykke arbejde, inden metoden kan kommercialiseres.
Fremadrettet – et stort perspektiv
Hvis teknologien bliver implementeret med succes, kan det ændre, hvordan vindenergisektoren håndterer reparationer og potentielt reducere behovet for at kassere store komponenter.
-Disse løsninger giver os mulighed for at reparere indikationer direkte på produktionslinjen uden at skulle stoppe produktionen. Det gør, at vi kan lave hurtige reparationer i stedet for at kassere, siger Kaare Jensen videre.
Anders Vedel fra Vestas siger om fremtiden:
-Med implementering og udrulning, som forhåbentligt kan finde sted om tre til fire år, vil vi have noget, der gør en stor og meningsfuld forskel for hele industrien – både for underleverandører og OEM’er.
WeldCast-projektet startede i 2021 med partnere fra Siemens Gamesa Renewable Energy A/S, Vestas Wind Systems, BEATTR, FORCE Technology, DTU – Danmarks Tekniske Universitet og Energy Cluster Denmark. Projektet er finansieret af Innovationsfonden.